1. Why do we propose the reuse of textile wastewater?
The strong development of human economy and society has gradually depleted natural resources. Environmental pollution, climate change, …
We have become more aware of this problem and are promoting the issue of reuse. Not only recycling paper, plastic, metal, … but people are also recycling wastewater for reuse, circulating water in production, using clean energy such as solar, wind, garbage, …
Therefore, we mention the solution of reusing textile wastewater for the production industry that consumes a large amount of water.
2. Where do pollutants in the textile dyeing industry come from?
- The Sizing stage produces waste mainly starch, which reduces the concentration of dissolved oxygen in water. When anaerobic decomposition occurs, it will create an unpleasant odor including CH4, NO2, NH3, H2S
- The Weaving stage mainly causes noise and smoke, dust
- The Cooking stage uses high temperatures for the boiler area, bleaching machine, washing and dyeing, steaming, drying
- Washing and bleaching: organic radicals combine with metal ions to form compounds, mixtures that cause cancer, affecting human health and the environment. Including: H2SO4, NaOCl, NaCl, Na2SO4, Na2S, Na2S2O4, Non-ionic detergents, aromatic compounds, impurities, …
3. Proposed solution for reusing textile dyeing wastewater by TVTS
In the 80s of the 20th century, the RO ROCHEM system was strongly applied by many countries in the treatment and reuse of textile dyeing wastewater. With its effectiveness on each project, up to now, RO ROCHEM membrane technology is still being applied more and more widely with many new features and higher treatment efficiency.
With our technology, we can directly treat textile dyeing wastewater to meet environmental discharge standards with a recovery rate of 60 to 80%.
To improve the recovery efficiency of the textile dyeing wastewater treatment system, we have designed additional basic treatment systems such as: chemical, biological, mechanical, … before the wastewater enters the RO ROCHEM system. This helps us improve the treatment efficiency of the entire wastewater treatment system to over 90%.
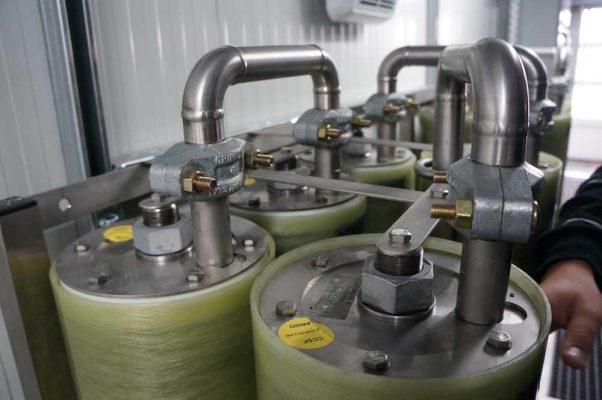
Currently, there are more than 1000 textile dyeing factories in the world that have installed RO ROCHEM systems. The table below shows some factories that have used our systems.
4. List of some textile dyeing factories that have installed RO ROCHEM systems for wastewater treatment and reuse
Factory name | Location | Capacity (m3/day) | Year |
SURIA FASHIONS | Tirupur, India | 150 | 2004 |
VICTUS DYEING | Tamil Nadu. India | 200 | 2005 |
AURO DYEING | H. P. India | 4000 | 2005 |
Creative Dyeing & Printing Mills | Faridabad, Haryana, India | 500 | 2006 |
Cheema Spintex Ltd. | Chandigarh, Punjab, India | 600 | 2007 |
Factory name | Location | Capacity (m3/day) | Year |
Abhishek Industries Ltd. | Barnala, India | 2500 | 2008 |
NTC Tender | Karnataka, India | 2800 | 2009 |
Technopak Singora textile | Ludhiyana,Punjab, India | 500 | 2010 |
Bhilosa Industries Pvt. Ltd | Silvassa, India | 1500 | 2011 |
Kanchan India Ltd. | Rajasthan, India | 700 | 2012 |
Aquachem Engineers P. Ltd. – For Grasim Vilayat | Mumbai | – PLANT A: PT: 2 x 5000W Raw water
– – PLANT B: PT: 2 x 3750W ETP Treated Effluent |
2011 |
Grasim Industries Ltd. Vilayat | Bharuch | ETP-36000 cum/day PT-RO I- 2 x 5000cum/day PT- RO II 2 X 3750cum/day | 2011 |
Tex N Nets | Haryana | 500 | 2011 |
Birla Cellulosic | Kharach, Kosamba, Gujarat | 5000 | 2011 |
Textile Consultant – Kejriwal Geotech | Surat | 1000 cum/day | 2011 |
To thoroughly treat the waste stream after RO, vaporization technology is the most effective and cost-saving choice. The concentrated stream with a TDS index of up to 20,000 ppm is a good and favorable condition for the vaporization system to maximize the recovery of clean water and create dry salt collected for landfill.
Based on advanced technology & techniques, TVTS is sure that when customers and partners come to us, they will always receive the values they desire as well as long-term, lifelong technical support services.